How LDPE gets recycled
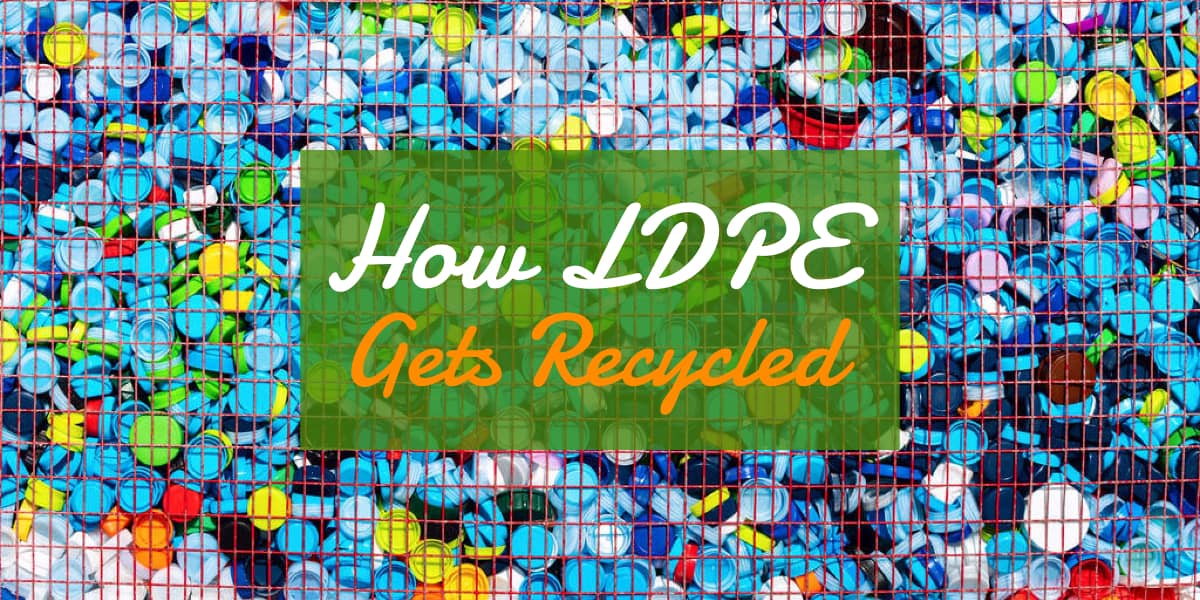
What Is LDPE Plastic?
Low Density Polyethylene or LDPE, is a type of plastic, used in everything from medical supplies to paper coating, is ideal for packaging applications, like plastic bags and milk carton liners. Because of its high flexibility, it makes up a significant portion of recycled plastics.
LDPE is one of the most widely produced plastics today. To produce the material, crude oil must undergo several steps, including cracking and polymerization. Once the process is complete, the resulting product is sent to a factory where it is extruded into thin sheets. These are cut into pieces and melted together into larger blocks. When cooled, the blocks become pellets, ready to be shipped around the world.
LDPE Plastic Recycling History
The LDPE plastic industry has seen tremendous growth since the early 2000s. This material is used extensively across industries like packaging, transportation, construction, retail, and consumer goods. In fact, according to Plastics Europe, global demand for LDPE grew by 8% in 2017 alone.
Because of its versatility, durability, and recyclability, LDPE is considered a “green” plastic. And while some plastics are simply burned off into energy, others are turned into products we use every day. For example, LDPE can be processed into bottles, bags, trays, and film.
But there’s still room for improvement. As many consumers know, most plastics end up in landfills, where they don’t decompose easily. They take hundreds of thousands of years to biodegrade completely.
That’s why most forms of PE recycling has taken off. Companies around the world are developing innovative technologies to recycle this material into new products. Some of those innovations include extrusion blow molding, coextrusion, injection stretch blow molding, thermoforming, and compression molding.
HOW IS IT RECYCLED?
A Look Inside The Recycling Process Of Polyethylene Film
The recycling process of polyethylene film, or PE film, is very complex. In fact, there are multiple steps that occur throughout the entire process. These steps include but not limited to collecting, transporting, processing, and separating. Each step plays a vital role in making sure that the material is properly cleaned and sorted into recyclable materials.
Collecting
LDPE Film Recycling Businesses have done a great job setting up programs for collecting, baling and recycling their LDPE Film scrap. Distribution centers lead collection efforts, then transport the collected scrap to consolidation locations, where it is consolidated and prepared for shipment to customers.
Grocery Stores have set up drop off boxes for residents to bring LDPE Film scraps from home for recycling. These boxes end up at the consolidation locations for baling and ends out being converted into new products. Farmers have invented machines to collect LDPE Film scraps directly from the fields. The key is to keep contamination levels low.
Transporting
Most plastic brokers and processing centers build a network of logistic providers that transport plastic scrap from all over the world. When a collections center or manufacturer has accumulated enough scrap, long haul trucks retrieve the plastic. From there they are brought directly to a processing center or to a larger collection facility for international shipments by boat.
Processing
When the film reaches the facility, it is brought inside. The outside of the building is covered with tarps to protect the equipment from weather conditions. Once inside, the film is inspected. Inspectors check the quality of the film and ensure that it meets certain standards. If it does not meet those standards, it cannot enter the recycling process.
Separating Plastic Materials for Recycling
To recycle plastic film, it must first be separated into two types — HDPE and LDPE — and then colored or printed. If film is not separated from the plastic, it can greatly affect the value and quality of the products made with the recycled plastic. Colored or printed film and clear film go to different processing streams because otherwise they could contaminate each other’s processing streams, which would greatly diminish the value of the end product.
Other items that need to be separated are films with labels and films without labels. Technology is available in the United States to clean labeled films before moving them on in the recycling process Recycling more film domestically means that less film needs to be shipped overseas.
How Does the LDPE Plastic Recycling Process Work?
LDPE film gets shredded into flakes with grinders. Once in flake form, the plastic gets cleaned to remove dirt, contaminants and other debris. The cleaned flakes are then dried, melted and turned into pellets for ease of handling.
Then, the pellets are mixed with virgin LDPE and extruded into sheets or pipes. Other companies take the recycled material and combine it with virgin LDPE to make new product lines.
Next, the flakes go through a cleaning process where they are washed and filtered to remove impurities like dirt, dust, sand and other foreign matter. Finally, the flakes are dried and placed inside large bins.
When the flakes are ready, workers load them onto conveyer belts and drop them into melting machines. Here, the plastic melts down into molten liquid. The molten liquid is poured into molds to solidify into pellets.
These pellets are then shipped off to customers around the globe. They can be used to produce new products or sold directly to manufacturers. Some companies even sell the pellets to farmers to grow plants that eat plastic.
What Are the Benefits of Recycling LDPE?
Beyond reducing waste and creating a clean environment, there are practical benefits to recycling LDPE film. Companies that use recycled LDPE film save money on waste disposal and reduce the amount of garbage they send to landfills. And because LDPE is derived largely from natural gas, it uses less energy during production and recycling.
Use Recyclable LDPE Plastic in Your Processes
Chesapeake Materials is dedicated to sustainability and recycling LDPE plastic used for repurposing. We believe it’s important to make sure that every material we recycle meets industry standards and complies with environmental regulations. With that in mind, we supply recycled LDPE resin to ensure that our clients’ products meet those sustainability efforts.
Our team can help assess and determine the best way to incorporate recycled materials into your processes. Whether you’re considering using LDPE film for trays, bundling and shrink-wrapping, or picking and placing, our experts can provide advice and technical assistance. Call us today to discuss how we can help.
If you use virgin LDPE in your processes, reach out to our team to determine the best buying program to help your company create environment friendly waste streams, and increase profitably for your brand.